Few components are as critical as the steering knuckle in the world of automotive parts, especially suspension and steering systems. It supports the wheel hub, connects to the suspension, and transfers steering input—all under constant stress. Knowing what they’re made of isn’t just technical knowledge for anyone selling or servicing these parts—it’s the key to offering professional advice and building trust with your customers.
Let’s talk about materials — what goes into these essential parts, and why it matters more than ever.
Main Materials Used in Steering Knuckles
Steering knuckles are primarily made from forged steel, ductile cast iron, or aluminum alloys, each chosen based on a balance of strength, cost, and weight. Let’s break these down:
Forged Steel
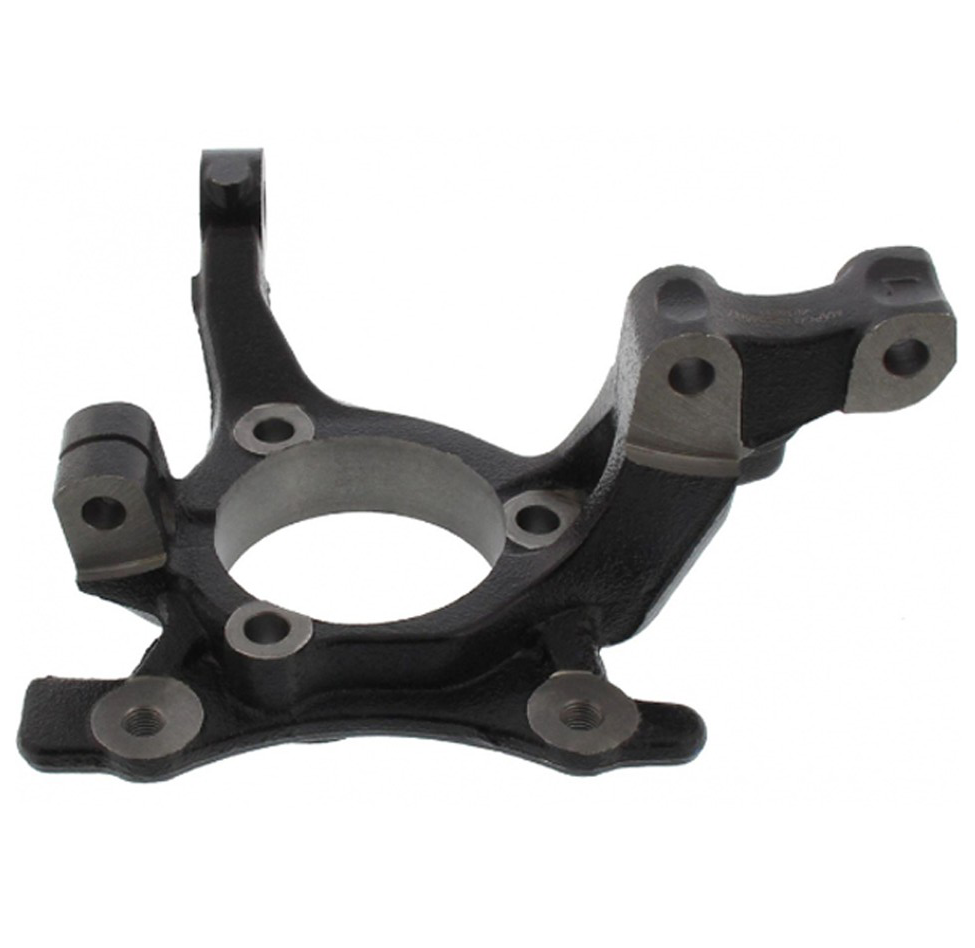
Forged steel is the strongest and most durable material for manufacturing steering knuckles. Its exceptional strength makes it ideal for vehicles subject to high loads and rough conditions, such as trucks and off-road vehicles.
Manufacturers often choose forged steel to make steering knuckles for heavy vehicles like trucks, SUVs, and dirt bikes because it offers excellent strength and durability. Although it weighs more than materials like cast iron or aluminum, the extra weight also adds to its toughness. Although it is more expensive to produce, the trade-off is long-lasting reliability.
In short, forged steel suits vehicles that need maximum strength, such as Silverado pickups and other large utility vehicles.
Ductile Cast Iron
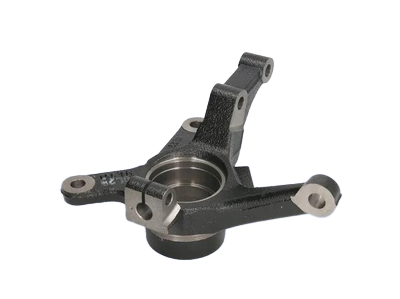
Ductile cast iron (Nodular Iron) offers a high level of structural strength while being more affordable than forged steel. It provides good resistance to stress and deformation, though it is slightly less robust than steel under extreme impact.
Sedans and midsize cars require less performance from the steering knuckle and place more value on durability, which is met by its workability and cost-effectiveness.
Aluminum Alloys
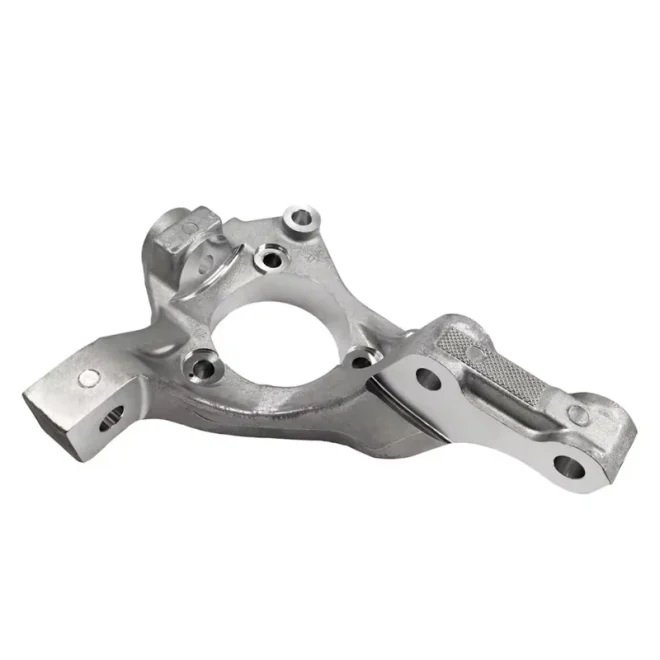
Aluminum alloys have gained significant popularity in recent years, particularly in modern passenger vehicles, electric cars, and performance models. Their key advantage is weight reduction. Aluminum steering knuckles can weigh up to 40% less than their steel counterparts, which directly improves fuel efficiency, handling, and emissions performance.
Modern casting and forging technologies have improved the strength of aluminum parts, making them suitable for front suspension systems in lighter vehicles. However, aluminum does not match the impact resistance of steel or cast iron and may be more vulnerable to fatigue or cracking under extreme loads or harsh driving conditions.
Still, when properly designed and reinforced, aluminum knuckles are a smart choice for reducing unsprung mass, a critical factor in ride comfort and responsiveness.
Material Choices for Different Vehicles
Not all steering knuckles are built the same, nor should they be. A Silverado 2500 hauling construction gear demands more than a city hatchback. Here’s how materials vary by application:
- Heavy-duty trucks and 4x4s: Prefer forged steel for durability and strength
- Mid-size sedans or crossovers: Often use ductile iron to balance performance and cost
- Modern EVs and performance cars: Favor aluminum for weight efficiency
For example, Silverado and F-150 models typically use forged steel knuckles due to their load demands. On the other hand, a Tesla Model 3 uses aluminum knuckles to reduce unsprung weight and improve handling efficiency.
Matching the knuckle to the use case is key, and a professional who knows the difference can provide much more accurate part recommendations.
Key Factors When Selecting Materials
Here’s where things get technical — and useful. When deciding which steering knuckle to use or recommend, professionals must consider several factors:
- Load-Bearing Requirements: Is the vehicle built for towing or hauling? If yes, go for steel or iron.
- Weight Sensitivity: Aluminum wins where reducing unsprung weight improves handling and efficiency.
- Environmental Conditions: Off-road use or high humidity? Steel resists deformation, while aluminum needs protective coatings to prevent corrosion.
- Budget and Cost-to-Benefit Ratio: Cast iron offers a cost-effective middle ground for daily drivers.
- Manufacturing Process Compatibility: Does the shop or supplier have tooling and expertise for machining a specific material?
Understanding these variables helps avoid mismatched parts and dissatisfied customers.
Understanding what steering knuckles are made of — and why it matters — gives you a serious advantage in the auto parts business. Whether it’s explaining why a Silverado needs forged steel or why a modern EV uses aluminum, mastering material knowledge means better service, smarter sales, and stronger customer trust.